INNOVATION – A New Standard in water processing
Using trusted technologies in a new way CS GAS innovated to create a new standard for water processing by combining multiple processes into a single road transportable package.
Location: Surat Basin, QLD
Industry: Coal Seam Gas Industry
Services: Engineering, Fabrication
Equipment: Waste fluid treatment services
The challenge
Treating workover fluid has traditionally been a costly and time-consuming process, requiring trucks to transport water to and from job sites. We were engaged by a major coal seam gas client to design and manufacture a solution for treating workover waste fluids with an objective to:
- Improve effectiveness of water treatment
- Increase speed of operations
- Fit the machinery within a single, non-piloted semitrailer
The dirty workover fluid needed to be processed into clean fluid. The criteria required it to be processed to a 99.8% reduction in total suspended solids (TSS) and a reduction in particle distribution size (PDS) down to five microns or lower.
The client nominated a sustained processing rate (of stream that flows through the system) of 880L per minute. The water requirements per workover were up to 350,000 L of clean water in (11 trucks) and up to 130,000 L (four trucks) of dirty water out.
The processing rate combined with the workover fluid specifications as well as having rapid deployment ability were unable to be achieved with any solution currently available. A new approach was required, while also working within significant constraints, including:
- Treating high quantities of water while adhering to guidelines set out by the Department of Environment, Science & Innovation (DESI) licence conditions and the Environmental Protection Act 1994 QLD.
- Performing advanced technical processes without the need for specialised labour and additional operational burden.
- Combining multiple processes, normally deployed in separate modules, into a single road transportable package.

Achieving these goals while working within the project constraints would exceed industry benchmarks. Although the industry has customised and optimised rig packages for high performance (with typical well to well turnaround times of two to three days), management of water and waste solids remained a logistical challenge.
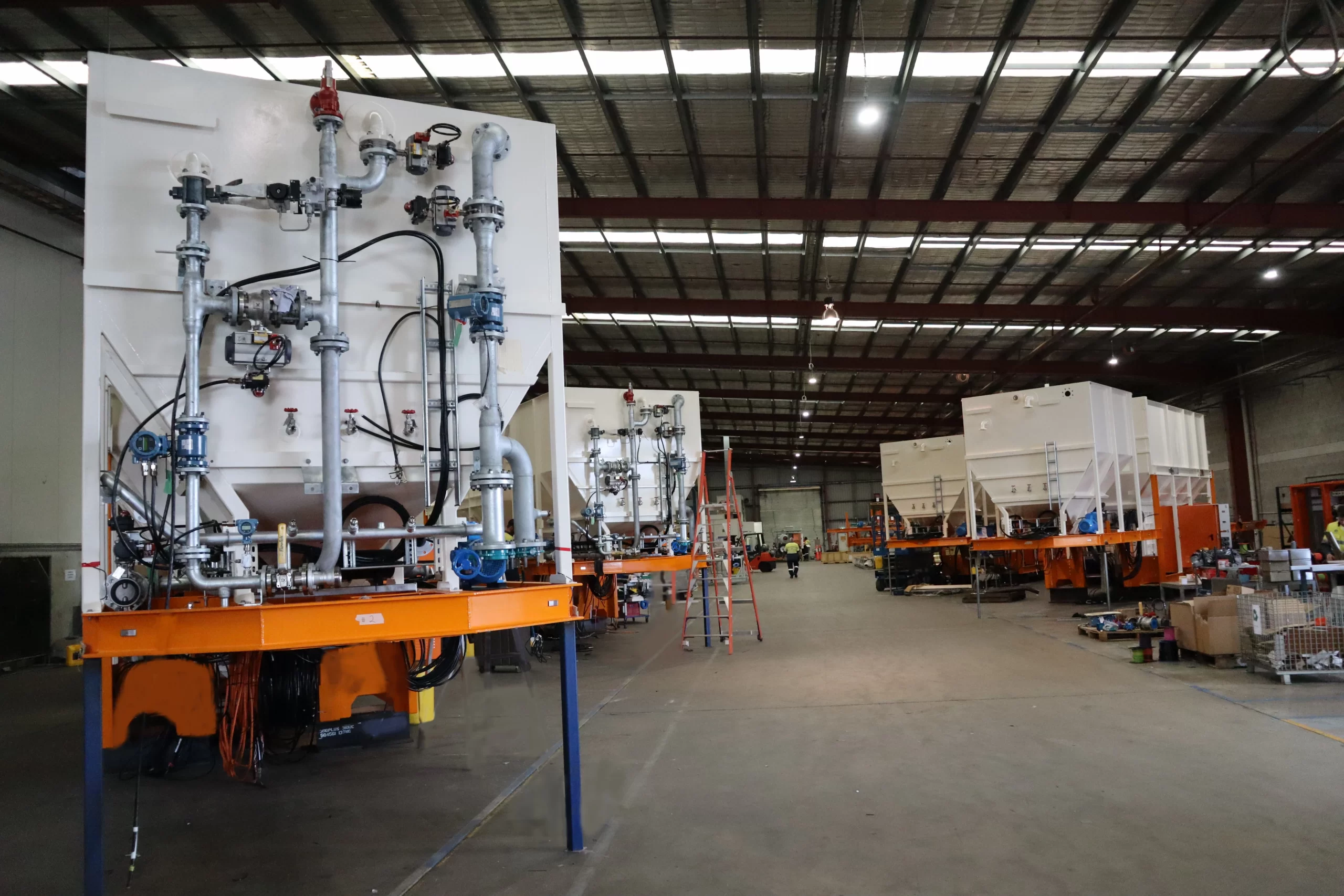
The solution
Our team designed and manufactured the WSTT in-house at our Acacia Ridge site, managing the project from inception to completion. We supplied all fabrication, E&I, automation control and remote operation as a turnkey solution, taking the following steps to ensure success.
- Piloting individual processes: We conducted pilot tests on a smaller scale to assess individual process success, which were then scaled up to simulate the final, full-sized unit, and performed thorough chemical dosing tests to determine the most efficient chemicals meeting specifications and environmental regulations.
- Taking a concurrent risk-balanced design approach: We initiated a parallel design, development, and build approach, fitting equipment parts into a semitrailer transportation envelope while refining sizes and specifications until all requirements were fulfilled.
- Developing a comprehensive control system: We created a control system enabling automated operation of the entire process with minimal operator intervention, integrating selected instrumentation to provide real-time data for automatic adjustments to accommodate varying inputs from clean water to slurry.
The outcome
The WSTT significantly reduced trucking operations, costs, non-productive time, water and wastewater requirements, improving safety, environmental and commercial outcomes and exceeded design specifications, including:
- The reduction of TSS to below 50mg/l, and exceeded the input design specification of 20,000mg/L, by more than a factor of 10 times (>200,000 mg/L).
- The unit can exceed the required sustained processing rate of 880L/min, and consistently achieved a rate of 962L/min.
- It fits within the dimensional and weight requirements of an unpiloted, road-transportable semi-trailer.
We have just completed our 100th workover on the initial project. The WSTT produced 53,926,000L (equating to 2,300 loads) of clean water that would otherwise need to be trucked in. Approximately 100 dirty truckloads of wastewater were saved on the project, or around one truckload per workover, and 762 tonnes of solids mass were recovered to be re-used or disposed of safely. The client also achieved a direct reduction in gross cost of $500k monthly by removing three water trucks from the permanent fleet.
Trucking operations for CSG workovers were cut down by reducing 2,991 driving hours, enhancing safety for the project team and the community.
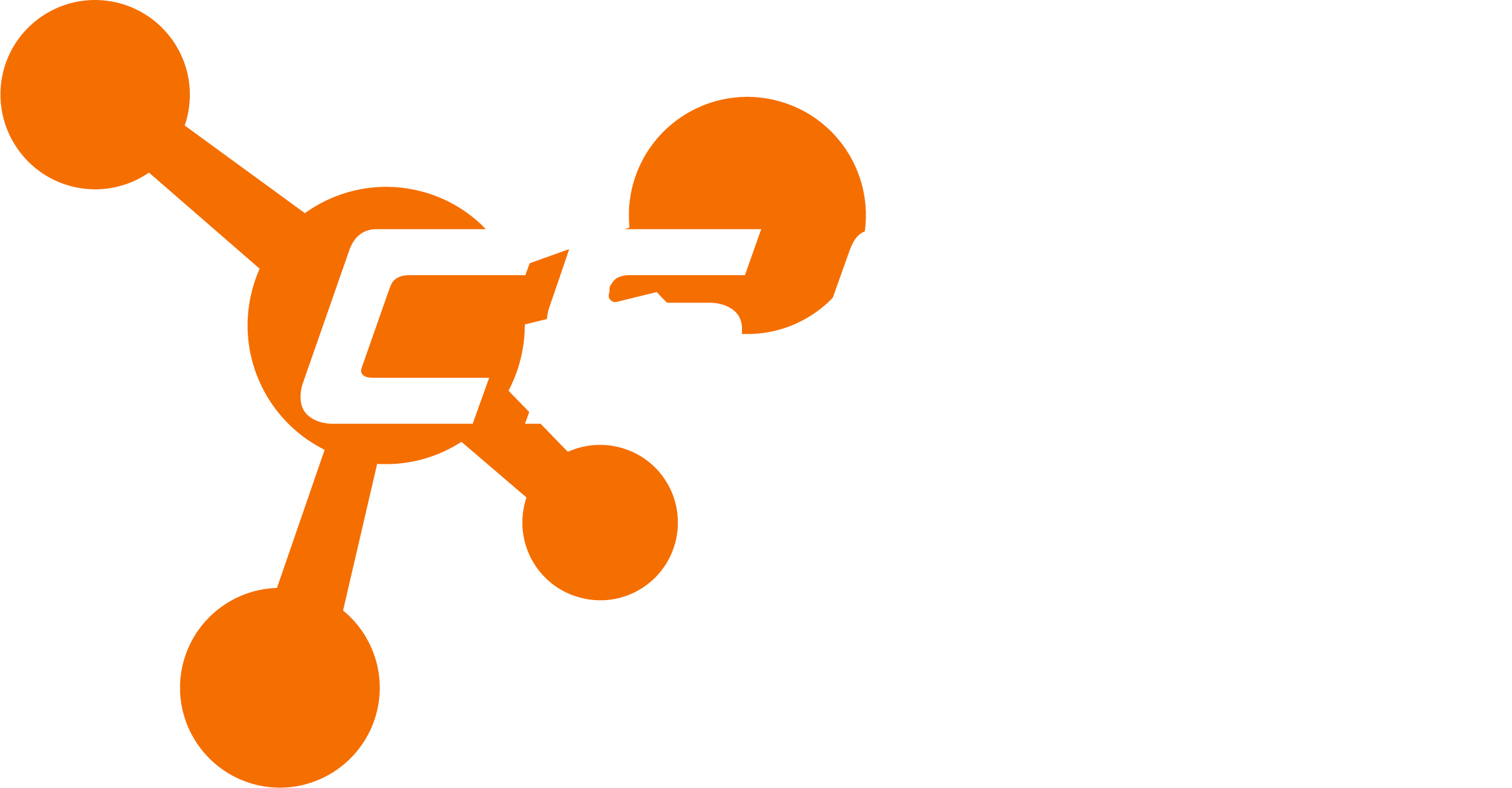
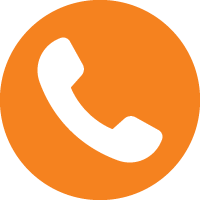
+61 7 3273 4222
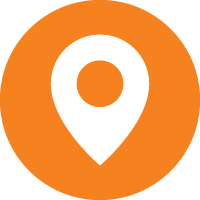
14A/243 Bradman St,
Acacia Ridge Qld 4110
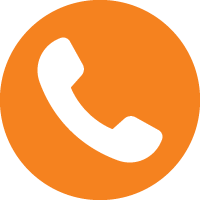
sales@csgas.com.au
Follow us
Qld Electrical Contractor Licence Number 71421 | NSW Electrical Contractor Licence no. 386286C | QLD Labour Hire Licence: LHL-04228-JRR8S
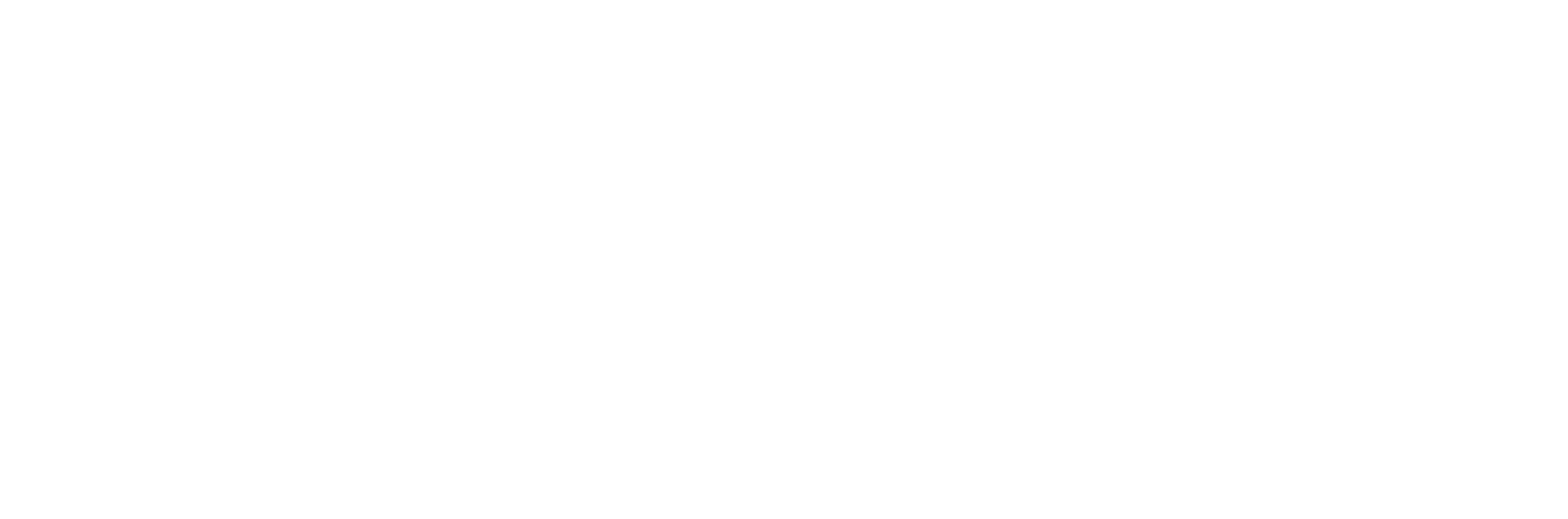